トヨタ生産方式に転機、在庫持ち始めた自動車業界――ジャストインタイム方式、コロナ下の供給網ひっ迫で見直し加速
トヨタ自動車は一部の部品を最大4カ月分備蓄している。独自動車大手フォルクスワーゲン(VW)は独自の車載電池を生産するために6カ所で工場を建設中だ。米電気自動車(EV)大手テスラは、かつてヘンリー・フォードがそうしたように、原料の入手ルート確保を目指している。
「ジャストインタイム」という言葉に象徴される自動車業界の超効率的なサプライチェーンは、約半世紀ぶりの変革を遂げつつあり、新型コロナウイルスのパンデミック下で起きたトラブルがそれを加速させている。需要の急な変動や異常気象、相次ぐ事故などを経て、必要なときに必要な部品が常に手に入るという大前提を見直し始めたためだ。
「ジャストインタイム・モデルは、サプライチェーンの効率化と規模の経済を意図したものだ」と日産自動車のアシュワニ・グプタ最高執行責任者(COO)は話す。しかし「新型コロナのような未曽有の危機で生じた波紋は、このサプライチェーン・モデルのもろさを浮き彫りにした」。
米国で高い人気を誇るフォード・モーターのピックアップトラック「F-150」を例に考えよう。新型モデルには、ガソリンと電気モーターを併用するハイブリッド駆動システムや、テスラ方式のソフトウエア自動更新といった最新技術が詰め込まれている。
コロナワクチンが感染を抑制し始める中、「F-150」の販売台数は今年1-3月期に約20万台と、同車種として13年ぶりの好調なスタートを切った。ただ、現在は供給が追いつかない状況だ。トラック工場の操業停止や生産制限は4月いっぱい続き、少なくとも5月半ばまで回復は見込めない。税引き前利益への打撃は最大25億ドル(約2730億円)に達する。
ジャストインタイムの基本的な考え方は、無駄を省くことだ。自動車メーカーは生産ラインで部品を取りつける数時間前か数日前にサプライヤーに納入させることで、未使用分が出た場合の費用を負担せずに済み、倉庫やその管理人員も節約できる。
だがサプライチェーンのグローバル化が進み、自動車各社が単一サプライヤーに頼るようになると、このシステムは次第に不安定になり、危機が起きる頻度も増えた。
テキサス大寒波
2月中旬、テキサス州を襲った記録的寒波と停電の影響で、米国で生産される樹脂の85%を供給する石油化学品工場の操業が停止した。樹脂は車のバンパーやハンドルなどの部品に使われる。車の原材料の中では最も安い部類に入るが、シートクッションにも使われており、ディーラーはそれなしに車を売ることができない。トヨタは3月末、原材料不足を理由に米国内の複数の工場で生産を停止した。SUV(スポーツ用多目的車)「RAV4」など人気車種の一部にも影響が出ている。

企業幹部によると、コスト削減効果が非常に大きいジャストインタイム方式を完全に改めるのは望ましくないという。だが最も脆弱(ぜいじゃく)な分野に絞ってある程度それを巻き戻すつもりだ。彼らが目指すのは、決定的に重要な部品の備蓄で、とりわけ半導体のように軽量で比較的安価だが、替えの効かない部品が焦点となる。
フォードのジム・ファーリー最高経営責任者(CEO)は、在庫量を増やすことを検討中だと述べた。「他業種の多くは半導体チップのような重要部品の安全在庫を確保している」。オートモーティブ・ニュース主催のイベントで同氏はこう述べた。「そうした企業の多くは生産能力が必要とする何年も前からチップに先行投資している」自動車業界に30年身を置くファーリー氏も、今年のような事態に備えていなかった。「供給基盤について学んだことの多さに、私は衝撃を受けている」と同氏は語った。
自動車業界で半世紀続いてきた慣行はEVシフトによっても見直しを迫られている。EVにはリチウムイオン電池や半導体など、供給不足が最も深刻な部品が多用されているためだ。
米ゼネラル・モーターズ(GM)と提携先の韓国LG化学は、オハイオ州に23億ドルの工場を建設中で、第2工場の建設用地を探している。年間数十万台のEVに搭載できるだけの電池を生産するためだ。独VWは合弁事業を通じて6つの電池工場を計画しており、2030年までに追加で140億ドル相当の電池を発注するとしている。
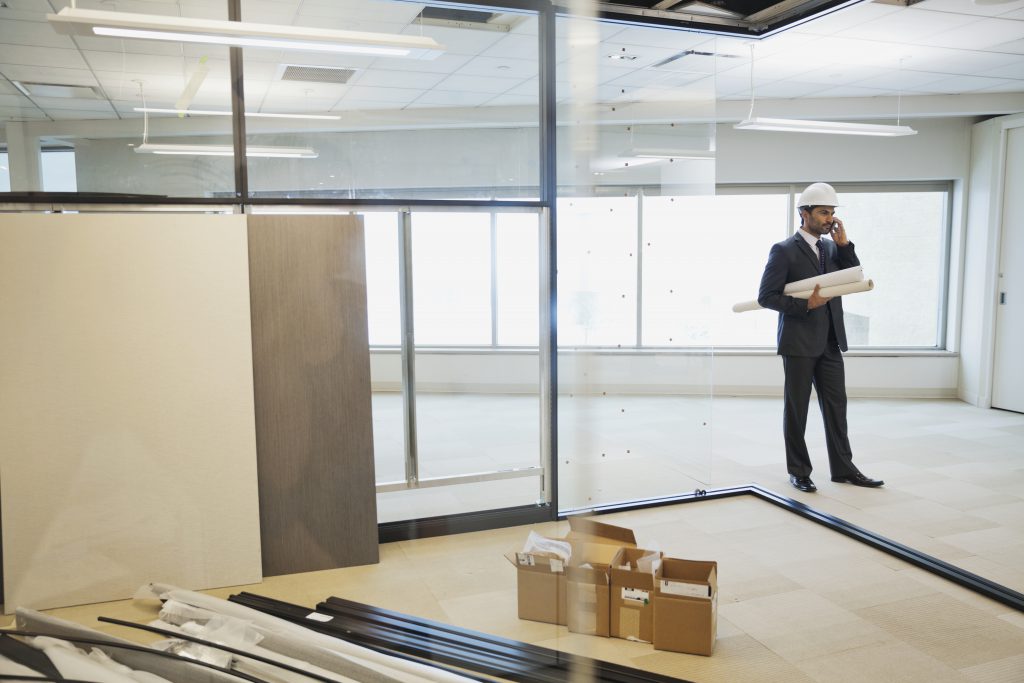
GMとVWはシリコンバレー流の経営手法をとるテスラの戦術を見習っている。テスラはパナソニックと共同でネバダ州の砂漠に50億ドルの電池工場「ギガファクトリー」を建設した。
もちろん電池の直接供給がサプライチェーンの問題を全て解決するわけではない。いかに斬新なEVであろうとも、フロアマットにはビニール、タイヤにはゴム、シートには革や布地が必要だ。
だがテスラは中でも最も戦略的な原材料を特定し、独自調達する方針を貫く。それは従来のジャストインタイム方式であれば、サプライヤーに任せていた仕事だ。昨年9月、テスラはノースカロライナ州で開発中の鉱山から将来リチウムを調達する契約を結んだ。
テスラCEOのこだわり
テスラのイーロン・マスクCEOは昨年、ニッケルも直接購入する意向を示した。「ニッケルを効率的かつ環境に配慮した方法で採掘するならば、テスラは巨額の長期契約を結ぶだろう」と述べている。
マスク氏の原材料へのこだわりは、自動車業界を100年前に押し戻す。当時、フォード創業者のヘンリー・フォードが考えた組み立てラインは製造技術の先駆けとなった。
1920年代、フォードが展開した最先端のビジネスモデルは「垂直統合」、すなわち自動車製造に必要な全てのものを管理する方法だった。本社を置くミシガン州ディアボーンのルージュ・リバー工場では、自動車だけでなく、フォード所有の鉄鉱山の産出物を原料にした自動車用鋼板も製造していた。
ヘンリー・フォードの死後、自動車業界では鋼鉄やゴム、輸送などはそれぞれ専門業者に任せるのが効率的だとの考え方が主流となり、メーカーは適切な部品や材料を購入し、それを組み立てるようになった。
次のステップを開拓したのがトヨタだ。1950年に米国のスーパーマーケットを訪れたトヨタの大野耐一氏は、陳列棚が空になると同時に補充されるのに驚嘆したとされる。倉庫が埋まるほど板金やタイヤを蓄え、生産ラインを止めないようにする自動車業界の慣習とは対極にあった。
これに着想を得て、後にジャストイン生産方式が考え出された。トヨタの工場に毎日大量のトラックがやって来ては1日の生産に必要な分だけを排出していく。
トヨタの工場の周りには「系列」と呼ばれる忠実なサプライヤーが集まり、それを簡単に実現できた。やがて効率性の高さが証明されると、米デトロイトから独ウォルフスブルクに至るまで自動車メーカーがこぞってこのシステムを採用し、大手サプライヤーやさらにその下請けにも波及していった。
他業種にもこの考え方が広まった。米アップルをはじめ、ファストフード大手マクドナルドのフランチャイズ店、米ターゲットなどの大型量販店が、在庫を少なく抑えるジャストインタイム方式を何らかの形で採用している。
ジャストインタイムと並行して、多くの自動車部品に単一サプライヤーが用いられるようになった。こうしたサプライヤーであれば、日々の納品状況を十分把握し、大量生産によるコスト削減や、自動車大手の世界的な工場のネットワークへの対応も容易になる。
欧州大手ステランティスのカルロス・タバレスCEOは3月のインタビューで、クライスラーやラム、フィアット、プジョーといった傘下ブランドで提供する100車種で推定約40万点の部品を購入するが、その95%程度を単一のサプライヤーから調達していると述べた。
「自動車業界では当たり前のことだ」とタバレス氏は語った。
2001年の米同時多発テロのような出来事で時折システムが混乱することはあっても、自動車業界は大抵、肩をすくめてしのいだ。慣行を続けることで得られる報酬が大きかったからだ。
だが世界金融危機をきっかけに潮目が変わり始めた。50社を超えるサプライヤーが倒産し、自動車メーカーは不意打ちを食らった。大手のビステオンの経営破綻では、同社に依存する自動車工場も操業停止に追い込まれるとの懸念が広がった。

一方、本家トヨタは別のショックに見舞われ、ジャストインタイムの再考を促された。2011年に発生した東日本大震災で、半導体大手ルネサスエレクトロニクスの生産拠点が被災するなど、サプライヤーが深刻な打撃を受けたためだ。
トヨタの広報担当者によると、震災後、同社はサプライヤーに部品の販売元を開示するように求めたという。こうした働きかけを通じ、トヨタは部品約40万点の詳細なデータベースを構築したと同社は話す。
備蓄にカジ切る
トヨタは一定の部品に関して、ジャストインタイムに反する備蓄をサプライヤーに要請した。最大手のデンソーは、財務資料によると2020年3月期の手持ち在庫を約50日供給できる数量に増やした。2011年は38日分だった。デンソーは在庫量に関するコメントを控えたが、緊急用の部品備蓄を、半導体を中心に始めていると述べた。
トヨタの取り組みは、今年の半導体不足を競合他社よりうまく乗り切るのに役立った。それでも完ぺきではなかった。10年前に被災したのと同じルネサスの工場で今年3月に火災が発生し、操業が1カ月間停止した。トヨタや日産などが全面支援しているが、同工場の完全復旧は7月頃になる見通しだ。
現在、多くの自動車メーカーは、かつてジャストインタイムを見習ったように、トヨタのネットワーク管理術に倣って隠れた弱点を見つけようとしている。
以上、Wall Street Journalより要約・引用しました。
https://www.wsj.com/articles/auto-makers-retreat-from-50-years-of-just-in-time-manufacturing-11620051251?mod=searchresults_pos1&page=1
おすすめ記事
-
1
-
独立社外取締役(コーポレートガバナンス・コード)について
コーポレートガバナンス・コード 2014年6月にとりまとめられた「『日本再興戦略 ...
-
2
-
独立社外取締役(コーポレートガバナンス・コード)の独立性基準について
独立社外取締役(コーポレートガバナンス・コード)の独立性基準 2014年6月にと ...
-
3
-
これまでの社外取締役/社外監査役の属性・兼任等の状況と、今後の 独立社外取締役(東証ベース)の選任についての調査・考察
株式会社コトラによる社外役員実態報告について 人材ソリューションカンパニーの株式 ...
-
4
-
職場の同僚と理解し合えないのは性格の不一致~人間関係に現れる価値観のちがい 組織理解vs他者理解~
職場の人間関係におけるアプローチについて、価値観の多様性から考えてみます。 相 ...
-
5
-
バブル体験の有無が価値観の差~70年代生まれと80年代生まれの価値観にみる世代ギャップ~
上司が、部下に的確に仕事をしてもらうために知っておくべきこと 「今の若いものは、 ...